KP Kleen Power
le migliori lavatrici sottovuoto
ad alcoli modificati
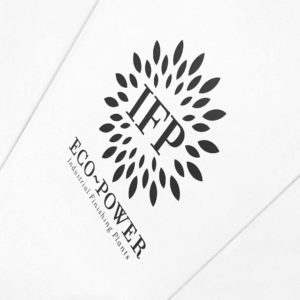
La gamma di lavatrici KP Kleen Power è perfetta per il trattamento di qualsiasi tipo di prodotto in metallo, di qualsiasi dimensione e complessità strutturale, contaminato da acqua, olii e scarti di lavorazione. Tutti i cicli di lavaggio vengono effettuati interamente in sottovuoto con l’impiego di ultrasuoni, di soluzioni detergenti acquose, alcoli modificati, idrocarburi o idrocarbuti hfe, sistema che garantisce una decontaminazione e asciugatura perfetta delle superfici metalliche, idoneo anche per i requisiti MOCA.
La tecnologia di KP Kleen Power è estremamente efficace sia per piccole che grandi quantità di prodotto da trattare, per qualsiasi dimensione e fattezza, anche per componentistica costituita da metalli diversi tra loro.
KP Kleen Power garantisce un notevole risparmio energetico, un recupero del 99% degli elementi contaminanti in linea con le disposizioni in tema di Economia Circolare, totale assenza di sversamenti di morchie o altri componenti nocivi e soprattutto garantisce la massima sicurezza per l’operatore.
Il lavaggio del futuro… adesso
RE-ACTION al B-62
C’è del nuovo nel segno dell’Evoluzione. Quest’anno al Mecspe 2024 siamo arrivati con una nuova macchina che ha portato un rinnovato entusiasmo e uno slancio verso la visione di una tecnologia 5.0 caratterizzata, tanto da un design ancora più ricercato, quanto minimalista.
Dix! Dieci anni di partnership tra C-Maj-Unics e IFP Europe
I dieci anni di partnership tra C-Maj-Unics e IFP Europe non rappresentano soltanto un anniversario a cifra doppia e tonda, ma anche e soprattutto dimostrano la forza della solida e proficua collaborazione tra le due realtà.
Apertura del Capitale agli Investitori Esterni: la nostra storia, le nostre scelte.
Un progetto di espansione raccontato al CUOA
Intervento di Giacomo Sabbadin, CEO di IFP Europe

KP Kleen Power 100% vantaggi
Riduce drasticamente il consumo di liquido di lavaggio
Abbatte i tempi ciclo e la potenza utilizzata dall’impianto con aumento del 100% della capacità produttiva
PRIMA
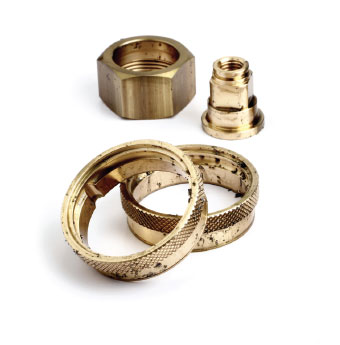
PARTI SPORCHE
+
LIMATURE
METALLICHE
+
OLIO CONTAMINANTE
+
PASTA DI LUCIDATURA
+
EMULSIONI
RISPARMIO
ENERGETICO
ATTENZIONE
PER L’AMBIENTE
BASSI
COSTI OPERATIVI
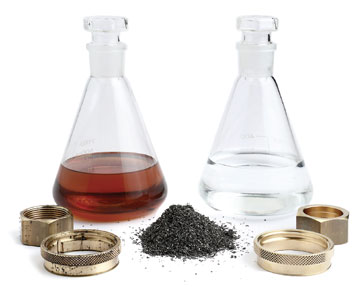
GRANDE VANTAGGIO
ECONOMICO
COMPARAZIONE LAVAGGI
DOPO
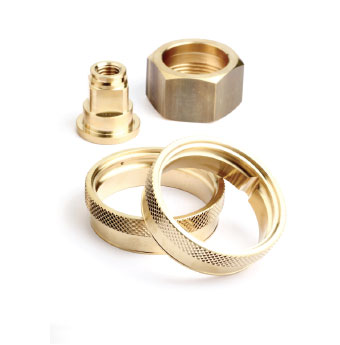
PARTI PULITE
+
ASCIUGATURA LIMATURA
+
RIUTILIZZO DELL’OLIO
+
SANIFICAZIONE
+
SEPARAZIONE
ACQUA / EMULSIONI
La miglior linea di lavatrici sottovuoto
KP Kleen Power
Tecnologia 4.0 / recupero scarti di lavorazione al 99% /
bassi costi di gestione / sicurezza per l’operatore /
4.0
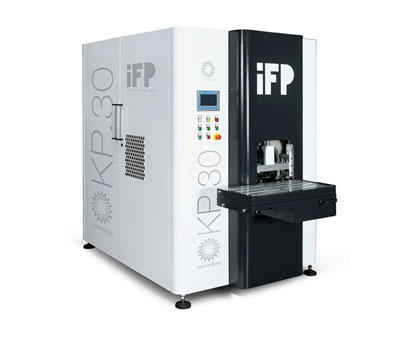
KP.30
30

KP.EASY
50 / 100 / 150 / 200
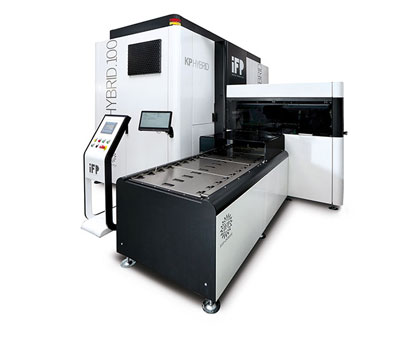
KP.HYBRID
30 / 50 / 100 / 150 / 200
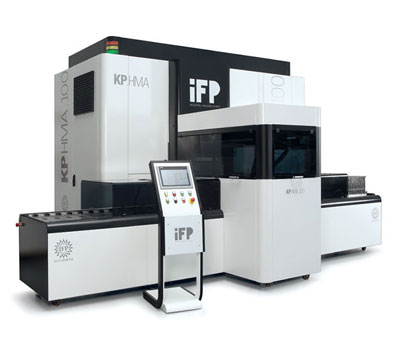
KP.HMA
50 / 100 / 150 / 200
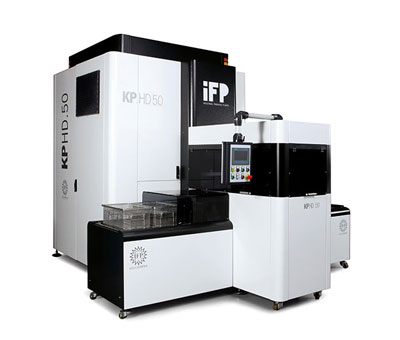
KP.HD
50 / 100 / 150 / 200
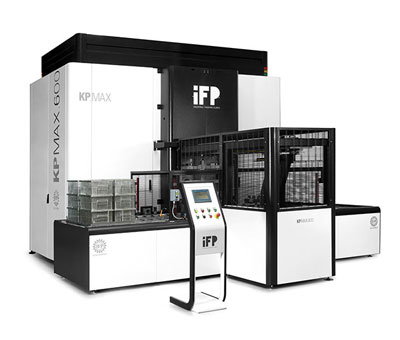
KP.MAX
400 / 600 / 800
Gli impianti della serie KPKleen Power grazie al ciclo di trattamento interamente sottovuoto fino a 1 millibar, rappresentano la miglior tecnologia di lavaggio presente attualmente sul mercato.
La combinazione dei seguenti sistemi di lavaggio in sottovuoto: soluzioni detergenti acquose, alcoli modificati, idrocarburi, idrocarbuti hfe, ultrasuoni, permette di sgrassare, pulire ed asciugare perfettamente ogni tipo di particolare.